What Is Lean Construction and Its Benefits?
Minimize waste, improve efficiency, and deliver quality projects faster with the Lean Construction method.
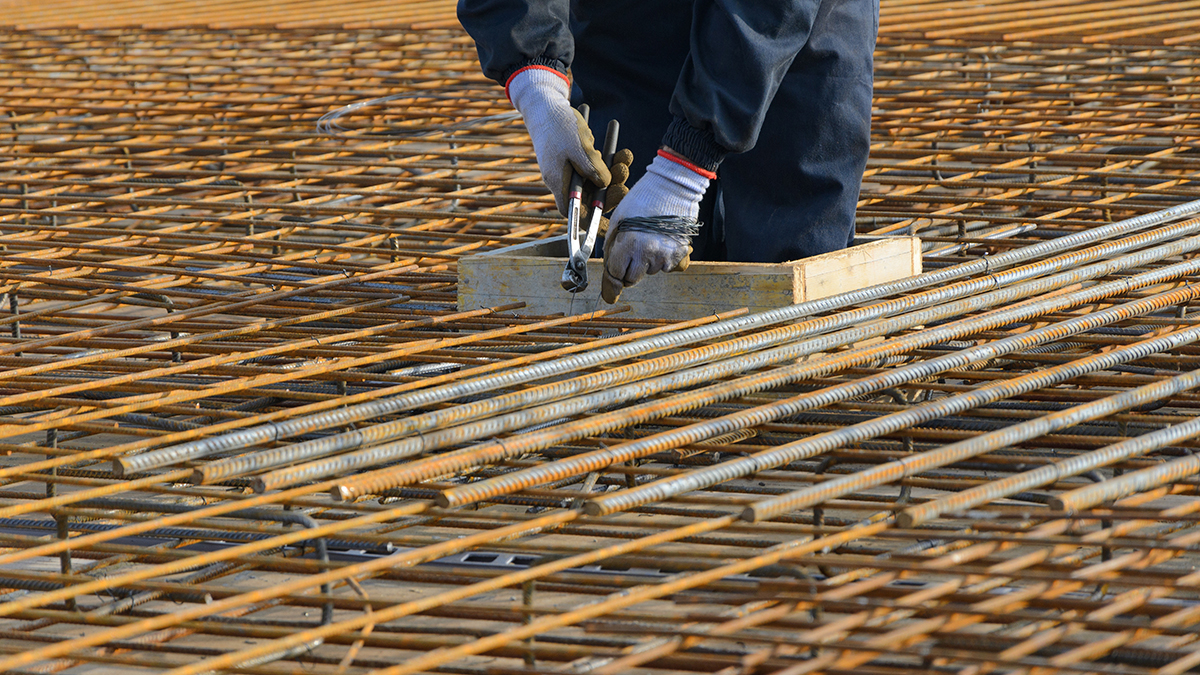
Low productivity due to inefficiencies is a common problem in the construction industry. To curb this problem and save money, many construction firms turn to lean construction.
Lean construction is a construction method that emphasizes reduced waste while maximizing stakeholder value. This type of construction is based on the Toyota Production method, which famously cut Toyota's production costs, while also resulting in better quality cars.
This method is intended to ensure maximum savings for construction companies and clients, but there is more than just one reason to engage in lean construction practices. Lean construction is safer, more collaborative, more environmentally friendly, and based on the idea of continuous improvement of all processes.
In this article, we'll explain the basics of lean construction, including its core principles and benefits. Construction companies often experience challenges when making the switch to lean construction, and this article will address those challenges as well.
What Is Lean Construction?
Lean construction is a method of building that minimizes wasted time, material, and effort. Lean construction maximizes value for the customer and improves the jobsite experience for everyone including contractors, facility managers, engineers, architects, workers, and more.
Lean construction targets waste in a variety of forms including:
- Overproduction: tasks are finished early and before the team can move on;
- Defects: work that is not done right the first time;
- Waiting: workers must wait for materials to be delivered;
- Transportation waste: materials are moved to the jobsite before they're needed;
- Underutilization of talent: a worker is assigned to a task that wastes their skills;
- Motion waste: objects or people are put in motion when it's not necessary;
- Over-processing: features are added that have no value to the customer;
- Inventory waste: excess materials sit around degrading because they are not being used;
Lean construction is a philosophy that also benefits the environment as well as the stakeholders and workers on the construction site. Lean construction eliminates waste on all sides.
Core Principles of Lean Construction
The core principles of lean construction include value generation, continuous improvement, collaboration, and waste reduction. These lean construction principles can be applied to construction in various ways.
Value Generation
Value generation is a commitment to delivering a quality product.
- Long-lasting product. Firms that follow lean construction strive to build structures that last as long as possible, to produce the least amount of waste.
- Deliver to specifications. Project managers, designers, architects and others work together to ensure the project is delivered to the client's specifications.
- Work together toward a common goal. All parties involved in a lean construction project have the same goal, and when they finish, all are able to agree that the goal was achieved.
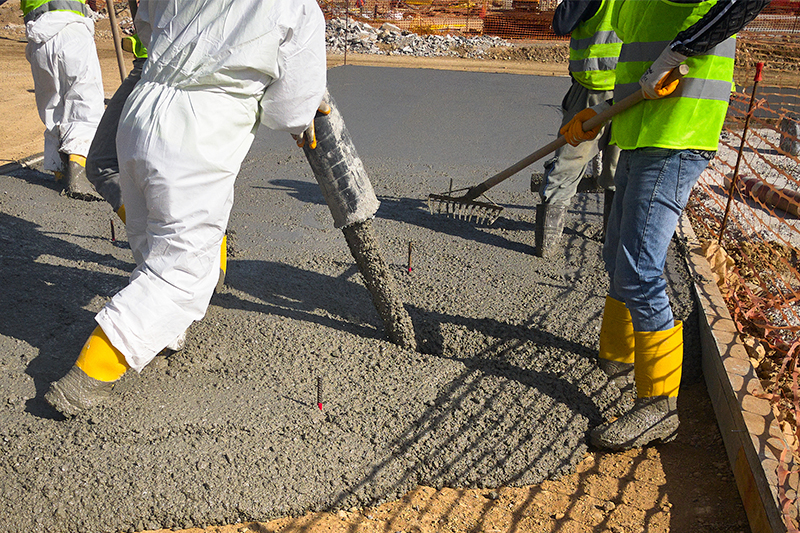
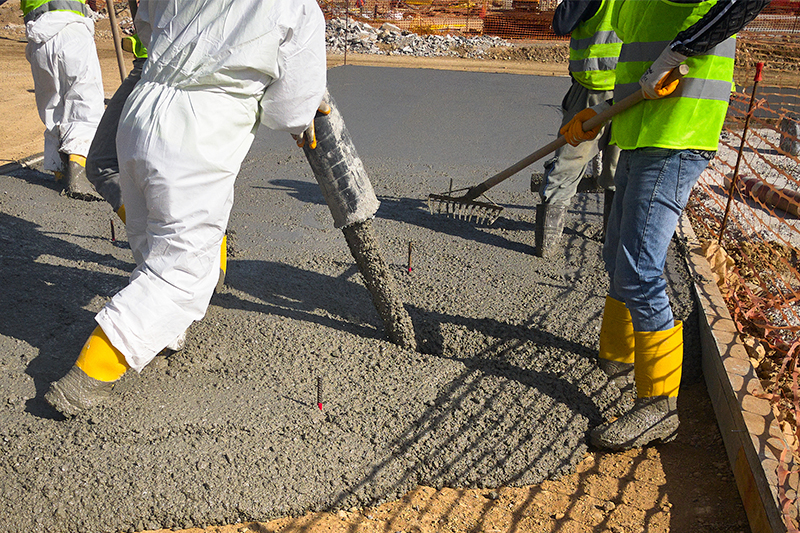
Waste Reduction
Waste takes many forms on construction sites. To reduce waste, construction managers must identify where waste occurs and find ways to eliminate it.
Wasted time
In 2022, contractors wasted up to $40 billion due to labor inefficiencies, and that number is believed to be on the rise. Time is wasted when workers are not able to operate efficiently, either due to a lack of materials, a lack of help, or other problems.
Construction managers can identify and eliminate waste in processes by stepping through these processes with workers and collaborating to identify solutions.
Erros also waste time. For example, a wall or window may be installed incorrectly. These errors must be repaired to ensure the structure is sound, which wastes time. It's better to identify methods to reduce errors. Giving proper training, greater oversight, and providing clearer designs are all ways to make this happen.
Wasted materials
Sometimes materials are wasted either because they don't last, or because an excess of materials have been ordered.
To minimize this type of waste, consider using durable, long-lasting materials like high-quality temporary fencing that does not need to be disposed of after one use. For example, instead of using sandbags, which quickly deteriorate, opt for reusable Anchor Bases to hold down fencing. This not only prevents waste but also ensures your fencing for the entire job.
Properly installed fencing will remain in place, saving crews time and effort.
Another way to avoid material waste is through better planning and just-in-time deliveries. This means ordering only what is needed and avoiding unnecessary excess. Assess material usage in advance to determine the required quantities before placing any orders, ensuring that materials arrive exactly when needed.
This approach saves money, reduces storage requirements, and prevents deterioration of materials due to weather.
Continuous Improvement
Problems are opportunities. Taking the time to review processes, identify areas for improvement, and implement changes can become a habit and a part of the organizational culture of construction companies.
If this is done frequently enough, problems can also bring together workers and managers from all parts of the organization. Working together to fix problems can help build trust and give each member of the team an opportunity to make a contribution.
Engaging in continuous improvement can also make the jobsite safer, reduce accidents and absenteeism and improve worker morale overall.
Collaboration
It takes teamwork and communication to make lean construction work. Collaboration brings workers and managers together in harmony and can ensure that everyone involved in projects is working toward a common goal. Good collaboration relies on good communication, which is also a necessary to reduce waste and ensure the construction firm runs smoothly.
Benefits of Lean Construction
There are many benefits of lean construction, including:
- Less waste. Lean construction management leads to less waste during your construction projects, from start to finish. You'll reduce material waste while simultaneously saving on labor. Lean construction is better for the environment and better for your construction company.
- Better project efficiency. Contractors that practice lean construction spend a lot of time evaluating their processes and jobsites to make their projects as efficient as possible.
- Cost savings. Improved efficiency means money is saved in many ways. Construction companies that practice lean construction enjoy opportunities to save money on materials, labor, error correction, and more.
- Improved quality. Lean construction practices improve construction quality over time.
- Enhanced customer satisfaction. Higher quality work means enhanced customer satisfaction.
- Faster project delivery times. Lean construction cuts waste, including wasted time. Practicing lean construction principles means your company can deliver on projects faster than ever. Over time, your business can service more customers and generate more profits.
- Safer work practices. Lean construction can enhance your jobsite safety, leading to fewer accidents and improved employee performance.
Common Challenges in Implementing Lean Construction
Although lean construction is good for construction companies, companies that switch to lean construction may encounter several challenges. Resistance to change is a primary concern.
Teams that are set in their ways may be resistant to learning new processes. Some workers may even react with mistrust, assuming that their performance is being judged.
This resistance can occur across the spectrum of stakeholders. Lean construction management only works if all stakeholders are invested in its success. Everyone must work together toward a common goal to ensure that lean construction is a success. If all stakeholders aren't on board with lean construction implementation, the process may fail.
Training and education is a must for any construction company hoping to switch to lean construction practices. In order to implement lean constructions successfully, workers and other stakeholders must understand both the goals and benefits.
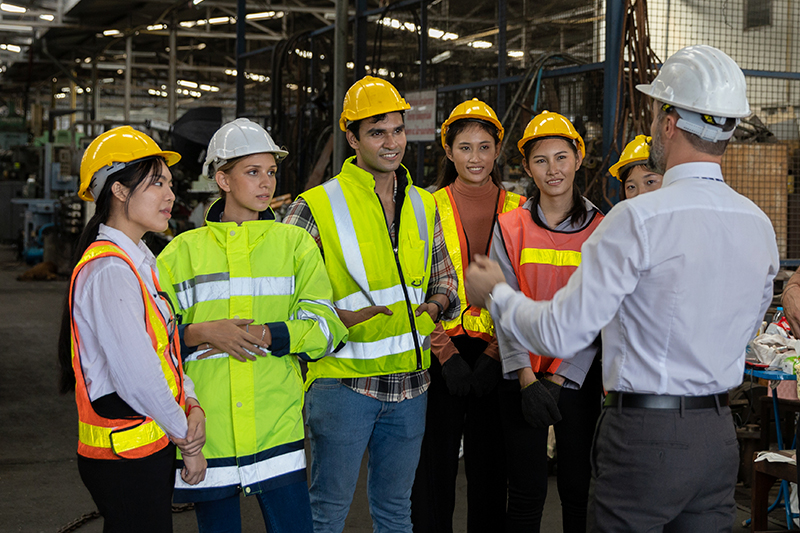
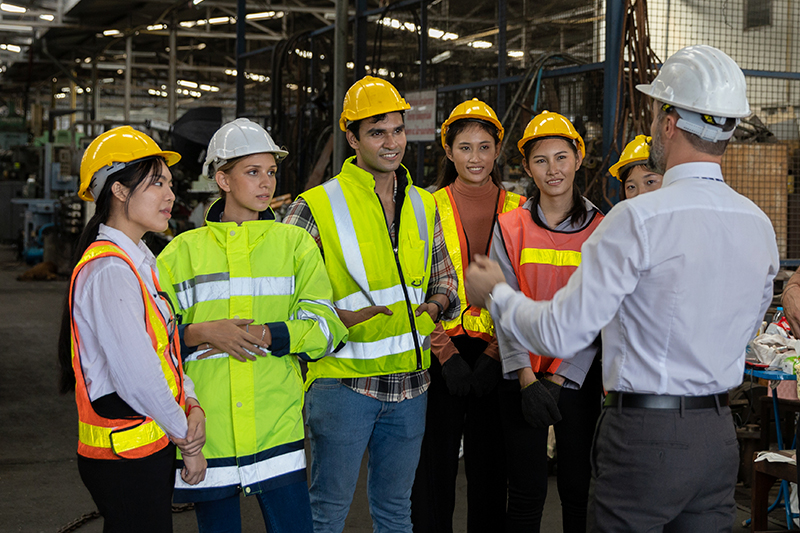
Strategies for Successful Implementation
There are many strategies for successful implementation. Some examples include:
- Involve all team members. Show your team members that they are a crucial part of the process. Begin collaboration with workers, managers, architects and others as soon as possible.
- Continuous training and education. Teach your workers and other stakeholders about lean construction principles. Doing so will help them understand why they're going through this change.
- Monitor progress and adapt strategies as needed. Perform regular inspections of lean construction processes to see how they're being implemented. Make changes as needed throughout the transition.
Building Sustainably with Lean Practices
Lean construction improves efficiency and reduces waste on your job site. This waste can manifest in many ways: wasted time, wasted productivity, and most importantly, wasted resources.
One example of how lean construction can benefit the industry—and the planet—is found in the world's sand crisis. A shortage of sand is expected to impact the construction industry in the coming decades.
Sand is a commodity that construction companies cannot do without, as it is used in concrete and other building projects. Only by changing their practices and reducing unnecessary use of sand can construction companies help prevent this problem from becoming worse.
Learn more about the sand shortage and depletion of natural resources caused by the construction industry. By taking lean management seriously, your construction company can help the environment, save money, and improve your quality of work -- all at the same time.
Trend now
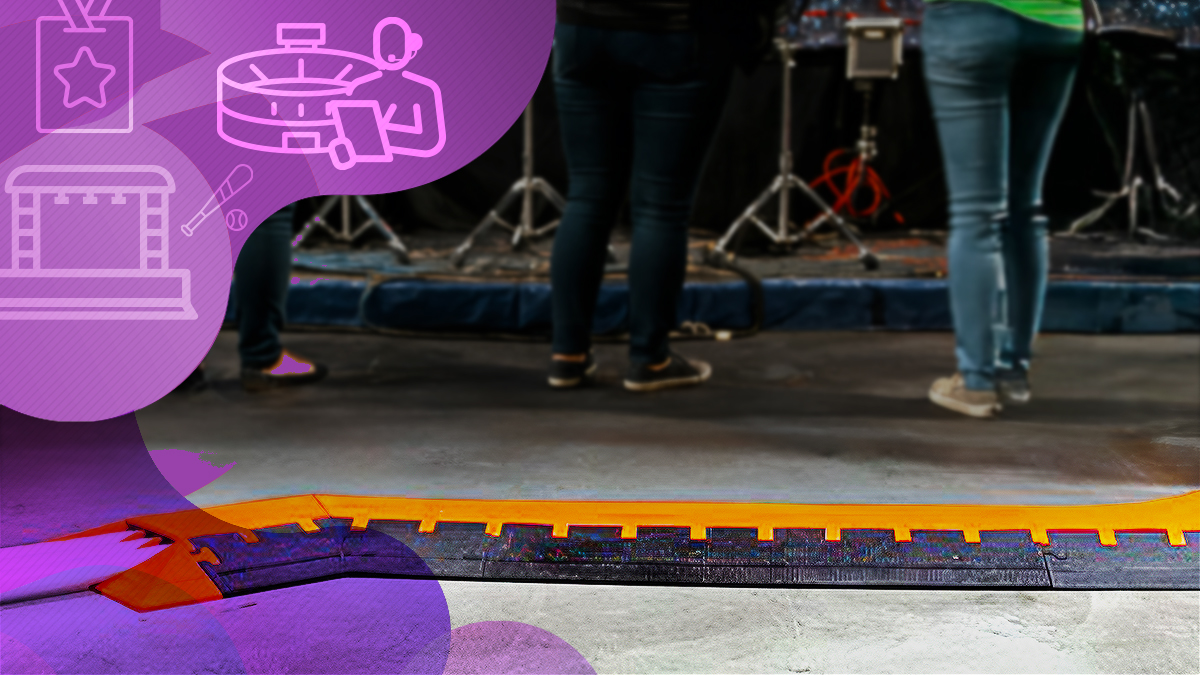
How to Choose Cable Protectors for Event Venues
Managing cables at large venues requires more than tape and luck. It takes the right protectors built for real-world demands.
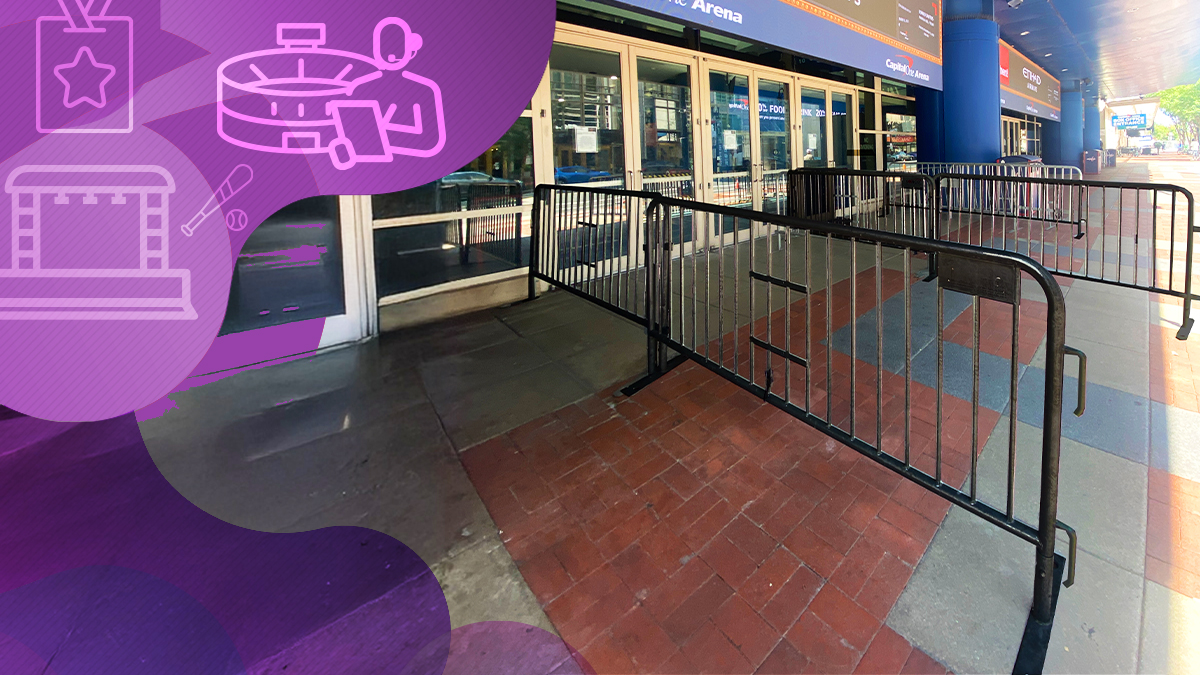
Best Crowd Control Barricades for Event Venues
If you’re planning events at scale, knowing what to expect from metal barricades can help you avoid common safety and setup pitfalls.
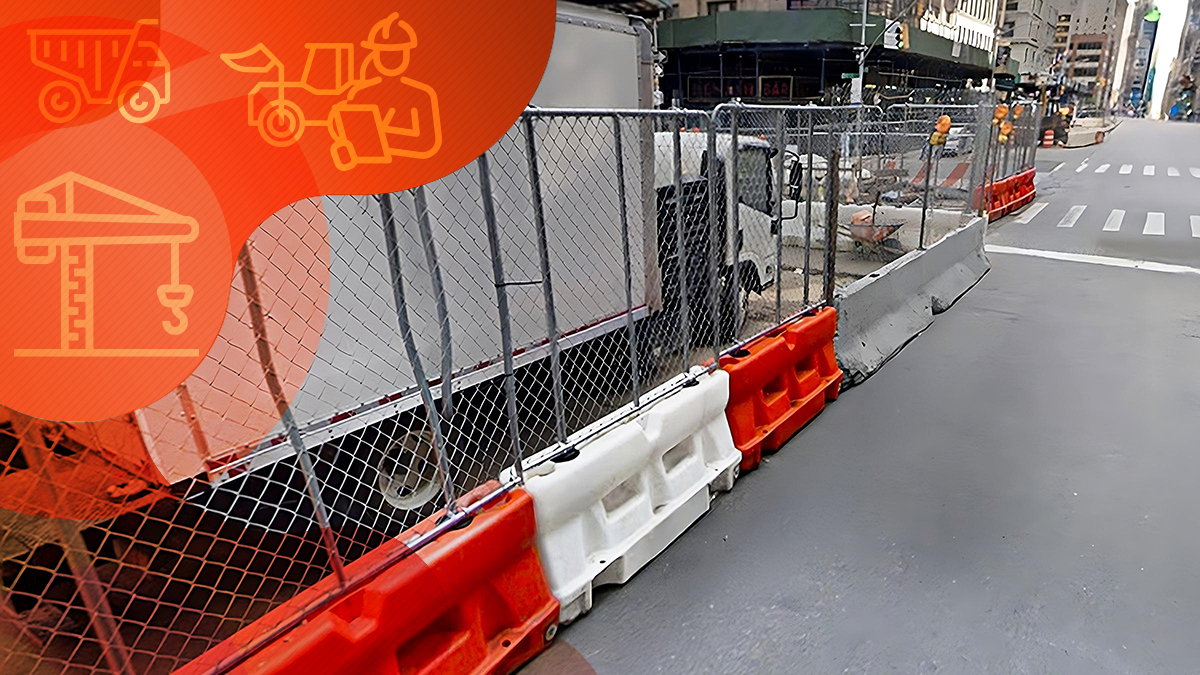
Choosing Between Concrete or Plastic Jersey Barriers
Not all barriers are built the same. Here’s what to know before choosing between plastic and concrete.